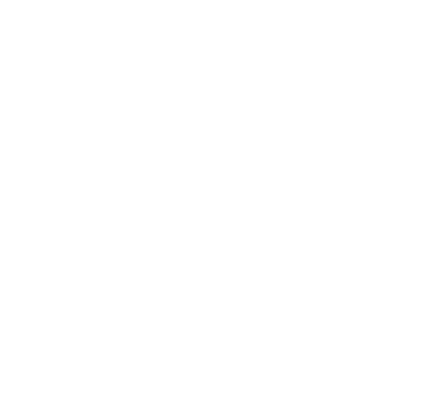
Новый
Уральские производители стройматериалов получили государственную поддержку
уровень
качества
3
«Известь Сысерти»
«АБСК-Системы утепления»
«Гросс-Групп ЕК»
На прошлой неделе в Екатеринбурге с размахом отметили День строителя — важный праздник для всех, кто привык создавать что-то новое и менять облик города. Поздравлять с профессиональным событием можно не только застройщиков, но и производителей стройматериалов, от качества которых зависит качество нашей жизни.
«Известь Сысерти»
«АБСК-Системы утепления»
«Гросс-Групп ЕК»
В этом году несколько предприятий этой отрасли стали участниками нацпроекта «Производительность труда», инициированного президентом страны. По программе проекта можно повысить эффективность работы, оптимизировать траты, устранить проблемы и наметить планы на дальнейшее развитие. В этом помогают инструменты бережливого производства: их внедряют на выбранном пилотном участке, а затем масштабируют на весь завод.
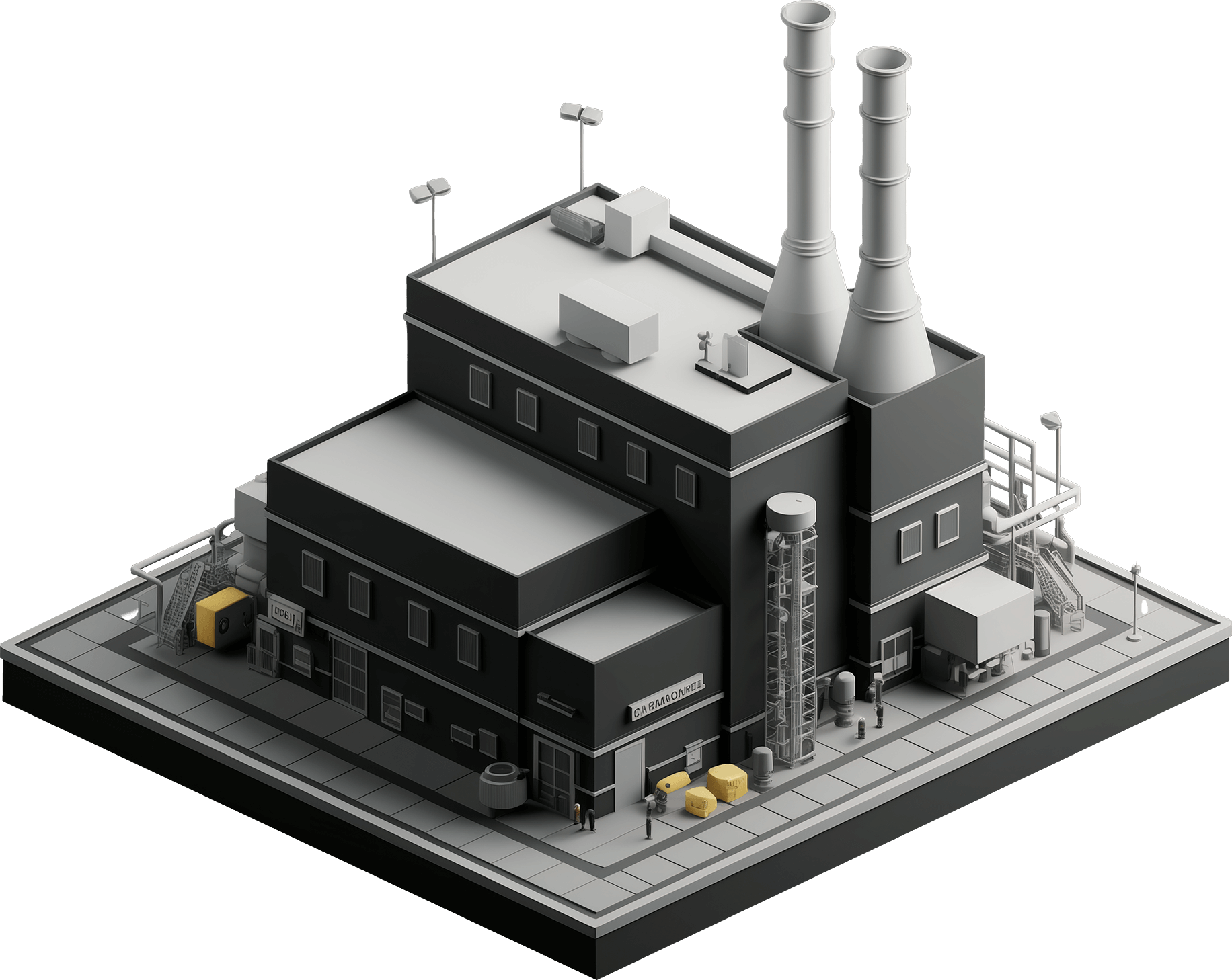
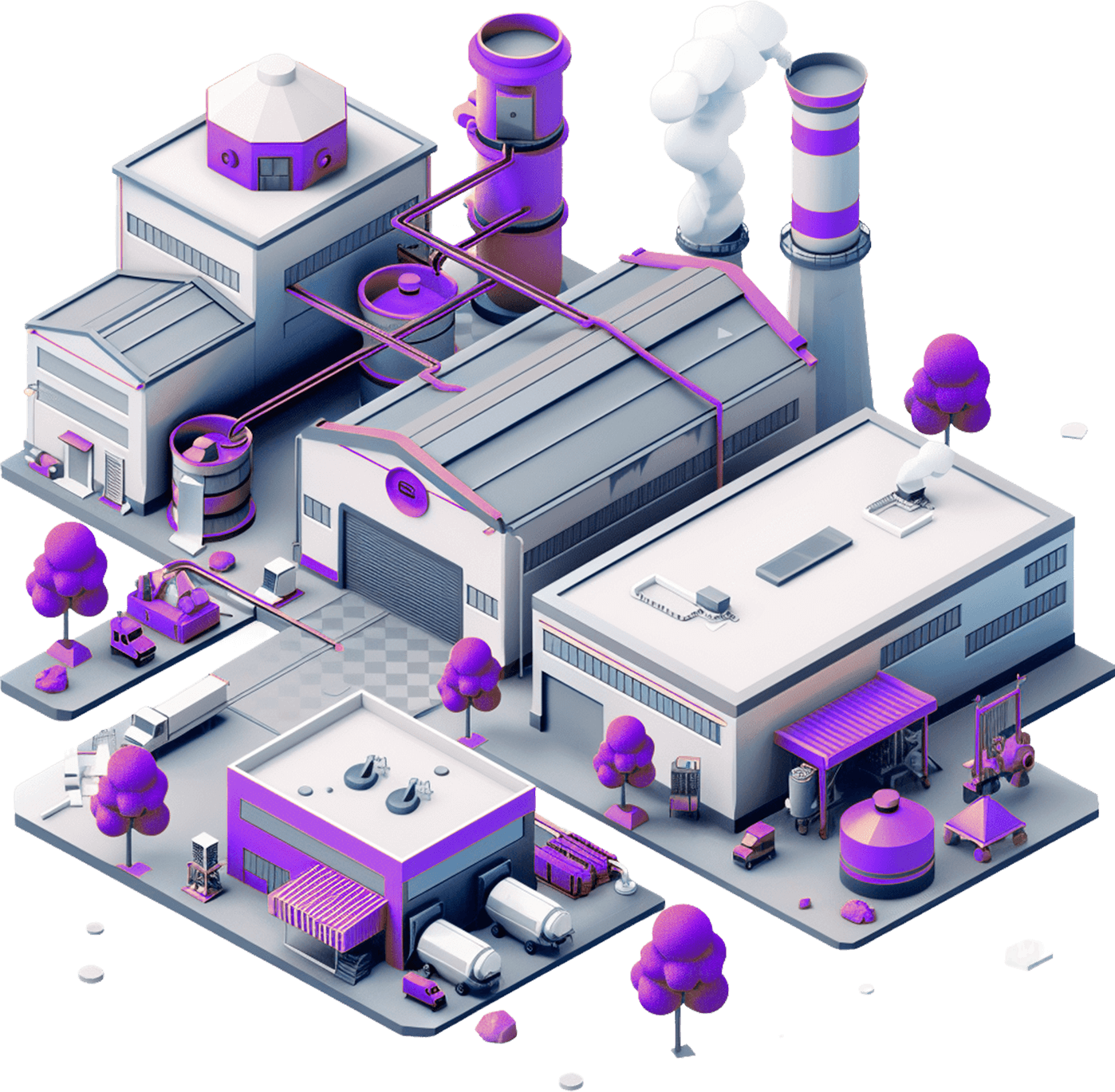
В Свердловской области проект реализует Региональный центр компетенций в сфере производительности труда (РЦК). Специально ко Дню строителя мы собрали истории трех участников, которые открыто поделились первыми успехами.
Разработали новую политику качества и увеличили выработку
Теперь точно в срок. Как производитель дюбелей наладил внутреннюю логистику и сократил простои
От «Спагетти» до «Автономного обслуживания». Что помогло сократить задержки в отгрузке бетона
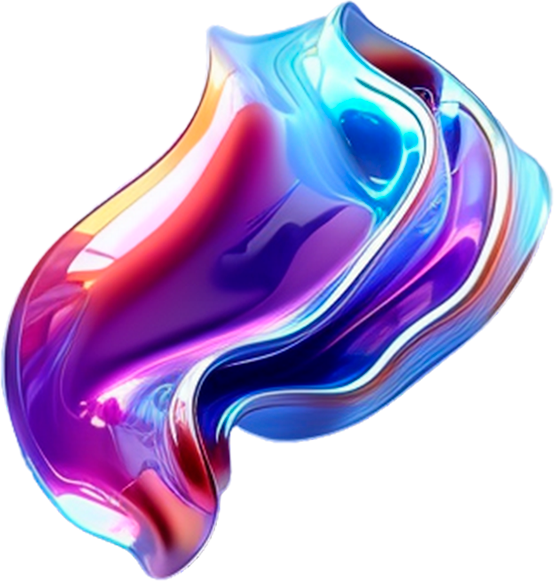
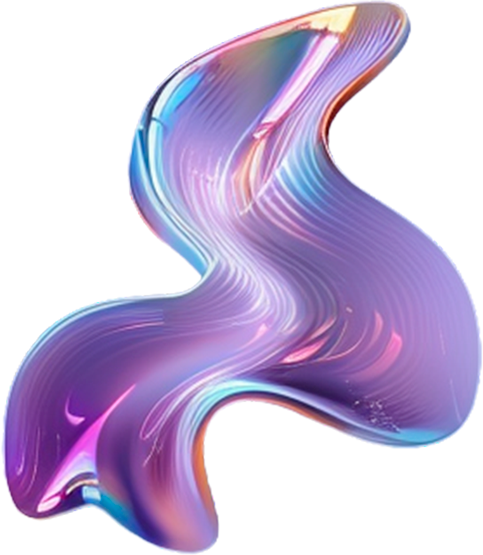
Разработали новую политику качества и увеличили выработку
Теперь точно в срок. Как производитель дюбелей наладил внутреннюю логистику и сократил простои
От «Спагетти» до «Автономного обслуживания». Что помогло сократить задержки в отгрузке бетона
Разработали новую политику качества и увеличили выработку
Производитель извести показал промежуточные итоги проекта
Завод «Известь Сысерти» — это уже шестое предприятие холдинга «Атомстройкомплекс», которое стало участником нацпроекта «Производительность труда». Каждый месяц на предприятии выпускают около 10 000 тонн продукции — качественной комовой и порошкообразной извести. Клиентами завода являются крупные металлургические предприятия УрФО.
— Мы поддерживаем идеи непрерывного совершенствования и постоянно ищем возможности для развития. На сегодняшний день «Известь Сысерти» является ядром кластера по производству строительных материалов в Сысертском районе, куда входят цементный завод и строящееся предприятие по выпуску автоклавных газобетонных блоков. Но еще в 2006 году, когда завод стал первым на территории индустриального парка «Габиевский», мы выбрали девиз «Не останавливаться на достигнутом!». Нацпроект «Производительность труда» — следующий этап модернизации производственных процессов, который точно не станет последним.
Виктор Ермолаев, управляющий директор, заместитель генерального директора управляющей компании ООО «Атомстройкомплекс-Промышленность»
Перед стартом активной фазы программы на заводе создали рабочую группу из наиболее вовлеченных специалистов предприятия и определили задачи будущих изменений:
- разработать политику в области качества;
- оптимизировать схемы хранения полуфабрикатов и методы контроля габаритных размеров горной массы;
- заменить часть оборудования на участке обжига.
Во время участия в нацпроекте заводу пришлось столкнуться и со своими сложностями, а точнее, особенностями, вызванными режимом работы: производственные линии действуют круглосуточно. Но в итоге это учли при определении оптимальных инструментов бережливого производства, и на практике сложностей уже не возникало.
Помимо «ОЕЕ — анализа общей эффективности оборудования», основными инструментами выбрали «Картирование», «Производственный почасовой анализ», «5С — организацию рабочих мест», «СР — стандартизированную работу». «Картирование» помогло проанализировать текущую ситуацию, составить перечень проблем, карту целевого состояния, найти решения и скорректировать цели проекта. «Производственный почасовой анализ» предоставил контроль за выполнением задания в течение смены с двухчасовым шагом, 5С улучшил организацию рабочих мест, СР дал возможность разработать стандарт операций.
По итогу реализации нацпроекта на заводе «Известь Сысерти» время протекания процессов снизилось на 23,3%, незавершенное производство в потоке — на 41,7%, а выработка увеличилась на 16,7%. Затем в течение 2,5 года наработанные методики завод будет тиражировать на остальные участки технологической цепи.
В качестве эталонного участка выбран один из важнейших цехов – цех обжига, где происходит термическая обработка известняка для получения высококачественной извести. Для оценки его деятельности применили один из самых распространенных инструментов бережливого производства – анализ общей эффективности оборудования, так называемый показатель ОЕЕ. Очень важно при расчете ОЕЕ опираться на точные данные, поэтому инструмент использовали специалисты, непосредственно отвечающие за эксплуатацию оборудования эталонного участка, – главный технолог и главный механик ООО «Известь Сысерти».
— Уже на этапе знакомства с предприятием был определен высокий уровень развития производственной системы — 17–18 баллов по нашему чек-листу оценки. Удивительно, но сложностей в реализации мероприятий не было, всё, о чем договаривались, полностью выполнялось. Команда проекта активно работала и помогала руководителю предприятия. С первых встреч у нас установились комфортная рабочая обстановка и конструктивное общение.
Александр Дикушин,
руководитель проектов РЦК
руководитель проектов РЦК
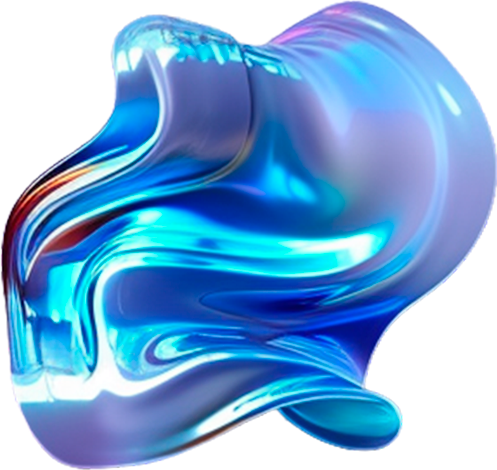
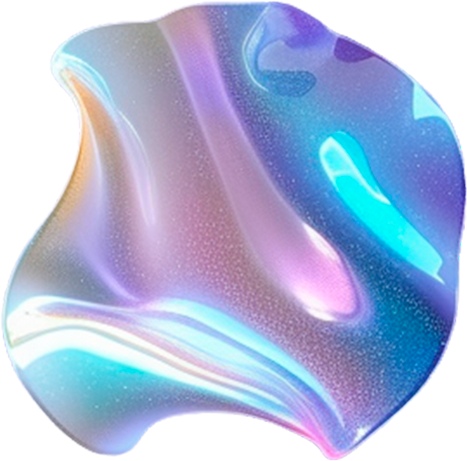
Еще до вступления в нацпроект на заводе создали свою систему решения проблем, но точечные решения для достижения целевых показателей сформировались в ходе совместной работы со специалистами РЦК.
— Другой эффективный инструмент — метод «5 Почему» — помог найти первопричину проблем. На практике это выглядит так: сотрудник сталкивается с нестандартной ситуацией и задает вопрос, почему она произошла. Найдя прямую причину, он задает следующий вопрос: почему возникла эта причина? Так выстраивается цепочка, в конце которой, в среднем через 5 вопросов, он находит истинную причину изначальной ситуации. Мы используем данный инструмент преимущественно там, где есть необходимость постоянного контроля качества извести, чтобы его уровень был неизменно высоким. Конечная цель на этом участке — разработка новой политики предприятия в области качества.
Виктор Ермолаев, управляющий директор, заместитель генерального директора управляющей компании ООО «Атомстройкомплекс-Промышленность»
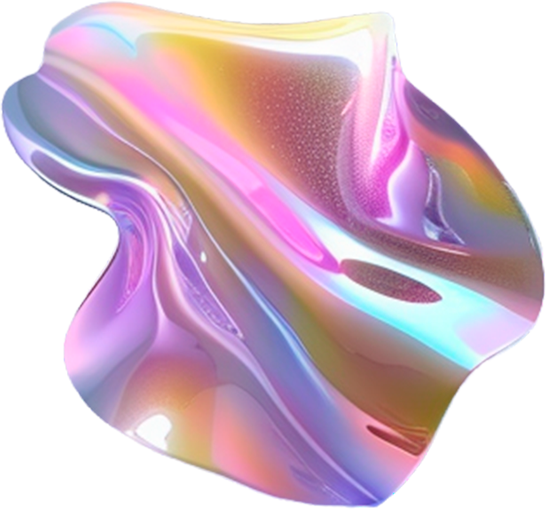
Внедрение инструментов бережливого производства всегда проходит с наставником РЦК, который помогает повысить уровень вовлеченности, потребность в совершенствовании руководителей и рабочего звена, а также показывает потенциал роста.
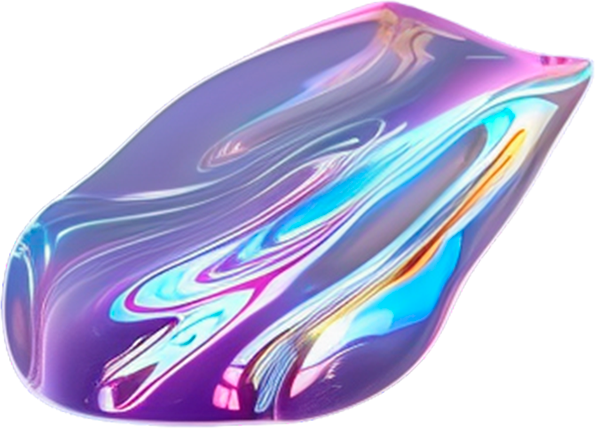
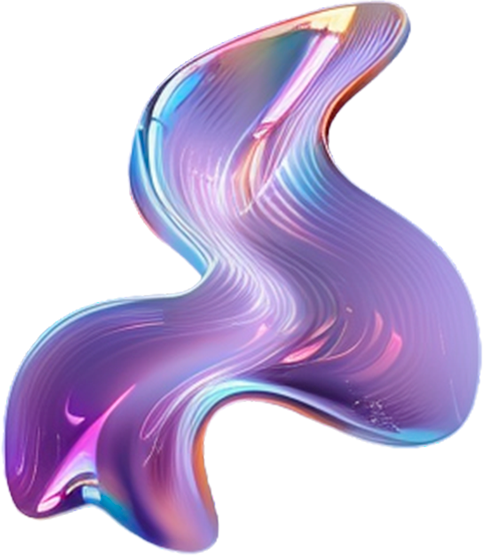

Тарельчатый дюбель BOGIRUS активно применяют в строительной сфере для утепления фасадов: 80% зданий в Екатеринбурге возведены с его использованием. Этот материал в уральской столице производит ООО «АБСК-Системы утепления». Продукция компании — комплектующие для фасадных систем, дюбели для крепления теплоизоляции, армирующие ПВХ-профили, штукатурные стеклосетки, анкеры для крепления подсистем. Также на предприятии недавно начали выпускать стеклоткани, которые активно применяют в строительстве для ветро- и влагозащиты зданий и сооружений, а также при производстве композитных материалов.
— Наша компания функционирует на строительном рынке уже более 10 лет. Мы продаем свою продукцию по всей России, от Калининграда до Владивостока, но Урал и Поволжье являются для нас ключевыми регионами. В нацпроект мы зашли для балансировки выпуска готовых изделий, чтобы в зоне переработки не накапливалась незавершенная продукция. Это приводит и к финансовым затратам: продукция просто лежит, и мы не можем продать ее клиенту.
Альберт Гайнулин, директор «АБСК-Системы утепления»
Сейчас участие компании в нацпроекте подходит к концу, итоги в цифрах подведут в конце августа. Но уже можно с уверенностью сказать, что инструменты и обучающие программы от специалистов Регионального центра компетенций позволили сократить время протекания процессов до 10%. И это еще не целевой показатель, есть над чем работать дальше.
На пилотном участке внедрили классический набор инструментов бережливого производства: «Картирование», «Спагетти», «Почасовой производственный анализ», «Стандартизированная работа», 5С, «Оптимизация переналадки», «Методика решения проблем». Первые три позволили зафиксировать ситуацию, сделать анализ и сформировать список проблем. С помощью остальных удалось подобрать необходимые решения для достижения целей проекта, построить карту целевого состояния и составить план мероприятий.
В ближайшем будущем на предприятии планируют внедрить систему наставничества с передачей накопленного опыта новым сотрудникам и тиражировать его на другие участки, чтобы производство стало систематизированным. По словам Альберта Гайнулина, вначале было сложно донести работникам важность участия в проекте и его цели. Но благодаря системе наставничества и авторитету руководителей это удалось сделать. Также регулярные обучения и беседы с персоналом проводили специалисты РЦК.
Сейчас участие компании в нацпроекте подходит к концу, итоги в цифрах подведут в конце августа. Но уже можно с уверенностью сказать, что инструменты и обучающие программы от специалистов Регионального центра компетенций позволили сократить время протекания процессов до 10%. И это еще не целевой показатель, есть над чем работать дальше.
— Самыми востребованными и понятными инструментами для сотрудников стали 5С, «Оптимизация переналадки» и система «Точно в срок», которые были наиболее быстро освоены и внедрены на рабочих участках. Плюсы очевидны: это визуализация, уборка рабочего места, уход за оборудованием, время перестройки и быстрая переналадка с одного ассортимента на другой, что позволяет точно в срок производить продукт, который востребован в данный момент.
Альберт Гайнулин, директор «АБСК-Системы утепления»
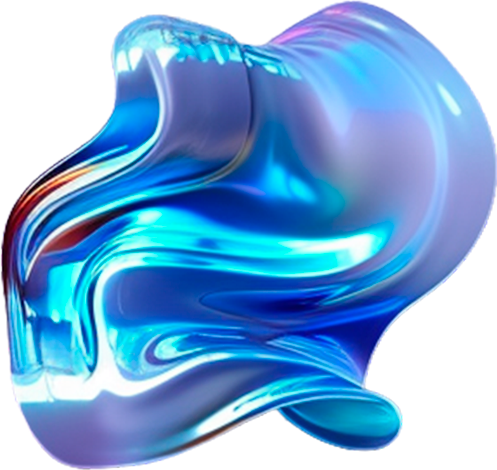
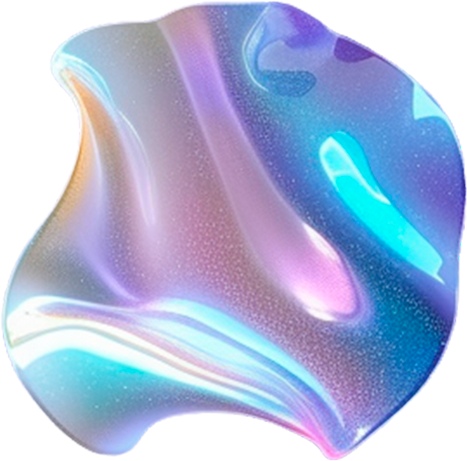
В качестве эталонного выбрали участок отливки термоголовок, так как он является наиболее трудозатратным. Именно здесь накапливалось наибольшее количество незавершенной продукции. Перед командой стояли непростые задачи: организовать ритмичную работу производственных участков по выпуску дюбелей и гвоздей, ввести эффективную систему производственного учета, сократить частые простои оборудования, снизить до минимума количество жалоб покупателей на брак и пересорт, наладить внутрипроизводственную логистику, связанную с хранением и получением сырья и готовой продукции, повысить вовлеченность персонала в производственный процесс.
— При реализации проекта мы столкнулись с такими сложностями, как риски ошибок, приводящих к массовому браку, при высокой скорости работы, «закатанные» в подсознании, постоянно повторяемые движения сотрудников при выполнении технологических операций несколько сотен раз в течение смены. Также выявили несогласованность планирования двух потоков, которые встречаются на участке комплектации и упаковки. Чтобы решить эти проблемы, мы обсудили и скорректировали шаблон планирования сменных заданий.
Александр Дикушин, руководитель проектов РЦК

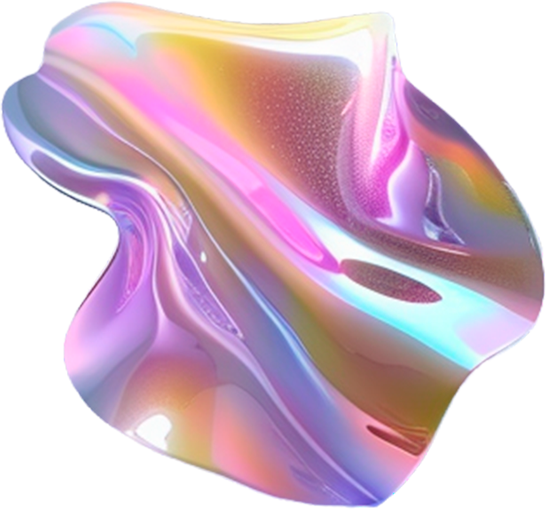
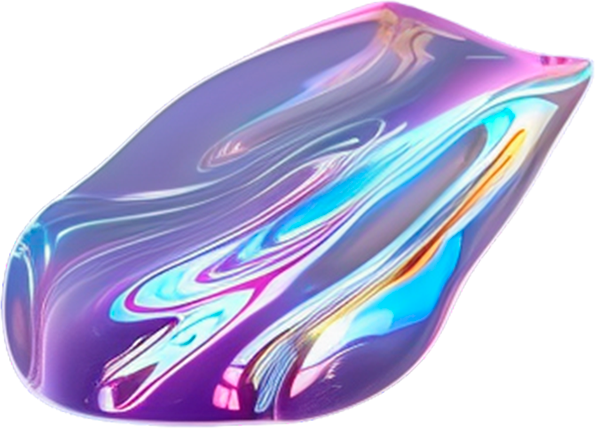
— На проекте сформировалась сильная духом и интеллектом команда, у которой есть огромное желание освоить на практике системный подход проектного управления изменениями. В итоге получилось реализовать даже больше мероприятий, чем мы планировали. Сотрудники «АБСК-Системы утепления» проявляют самостоятельность в поиске решений, у директора предприятия и руководителя проекта сформировались амбициозные цели.
Александр Дикушин, руководитель проектов РЦК
— Сотрудники поняли, что к нам приезжают заинтересованные люди с профессиональным подходом к работе и полноценным инструментарием. Когда собираешь узких специалистов в различных областях, у них не всегда получается взаимодействовать. Специалисты РЦК со стороны видят, что можно сделать, как сплотить команду и наладить производственный процесс. С их помощью сотрудники проявляют вовлеченность и инициативу.
Альберт Гайнулин, директор «АБСК-Системы утепления»
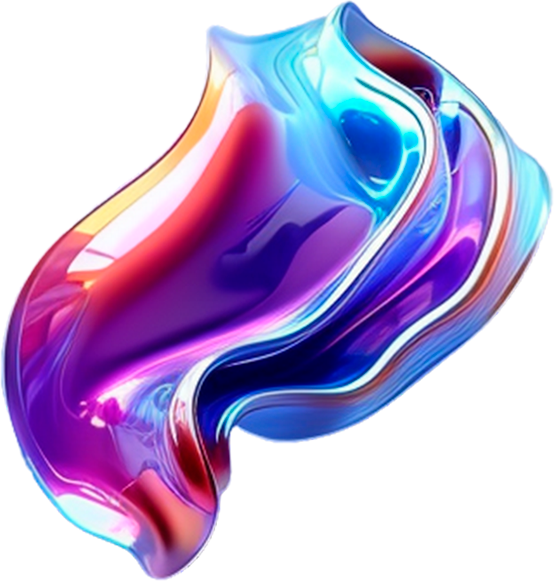
Теперь точно в срок
Как производитель дюбелей наладил внутреннюю логистику и сократил простои
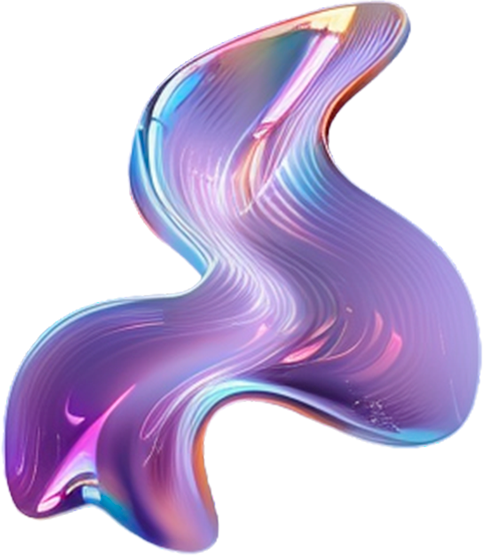
Сегодня в Екатеринбурге насчитывается порядка 35−40 бетонных заводов и узлов. Одним из лидирующих предприятий в сфере поставки товарного бетона является компания ООО «ГРОСС ГРУПП ЕК». Это ведущий поставщик товарного бетона разных марок и железобетонных изделий уже более 15 лет. Продолжая путь развития, укрепляя позицию лидера на рынке, ООО «ГРОСС ГРУПП ЕК» решили принять участие в нацпроекте «Производительность труда».
— В нашу группу компаний входят несколько заводов. Все выпускают одну товарную номенклатуру, работа построена по одному принципу. В национальный проект «Производительность труда» мы вошли с целью получения компетенций по бережливому производству на одном из участков и затем масштабировать их на все предприятия. План сработал: мы увидели конкретные результаты на первом заводе и уже начали внедрять lean-инструменты на остальных. Думаю, до конца года закончим эту работу. Суммарно она должна дать ООО «ГРОСС ГРУПП ЕК» значимый прирост эффективности и упрочить наши позиции на рынке.
Никита Калашников, исполнительный директор ООО «ГРОСС ГРУПП ЕК»
По словам Никиты Калашникова, инструменты, полученные от РЦК (Региональный центр компетенций — подразделение областного Фонда развития промышленности), — достаточно показательные. На их основе можно увидеть все пробелы, которые появляются по ходу решения основных задач. Раньше для их выявления требовалось больше времени, но теперь появилась возможность отследить и оперативно решить проблемы.
В качестве пилотного потока в ООО «ГРОСС ГРУПП ЕК» выбрали «Производство товарного бетона», доля которого в выручке от общего объема продукции составляет 71%. Здесь требовалось сократить время протекания процесса, увеличить производительность, выявить потенциал роста продаж и исключить риски невыполнения плана реализации товарного бетона.
В качестве пилотного потока в ООО «ГРОСС ГРУПП ЕК» выбрали «Производство товарного бетона», доля которого в выручке от общего объема продукции составляет 71%. Здесь требовалось сократить время протекания процесса, увеличить производительность, выявить потенциал роста продаж и исключить риски невыполнения плана реализации товарного бетона.
На старте проекта все участники рабочей группы прошли обучение по нескольким программам, и у руководителей их было больше, чем у рядовых сотрудников. На предприятии внедрили несколько инструментов бережливого производства: «Стандартизированная работа», «Почасовой производственный анализ», 5С, «Автономное обслуживание», «Картирование» и диаграмма «Спагетти».
«Картирование» и диаграмма «Спагетти» также позволили команде проекта под другим углом взглянуть на процессы изготовления и отгрузки товарного бетона заказчикам, пересмотреть организационные, технологические, логистические и информационные потоки, сопровождающие эти процессы.
Уже сейчас, до окончания первого этапа проекта, на эталонном участке организовали рабочие места в соответствии с системой 5С, стандартизировали порядок действий для оператора БСУ, внедрили «Почасовой производственный анализ». В итоге получилось достигнуть необходимых результатов по всем показателям пилотного потока.
Уже сейчас, до окончания первого этапа проекта, на эталонном участке организовали рабочие места в соответствии с системой 5С, стандартизировали порядок действий для оператора БСУ, внедрили «Почасовой производственный анализ». В итоге получилось достигнуть необходимых результатов по всем показателям пилотного потока.
— Самыми полезными для нас оказались «Почасовой производственный анализ», система 5С и «Стандартизированная работа». После тестирования инструментов бережливого производства на эталонном участке мы переносим их на другие бетонно-распорные узлы. А в следующем году хотим внедрить и на производстве железобетонных изделий.
Никита Калашников, исполнительный директор ООО «ГРОСС ГРУПП ЕК»
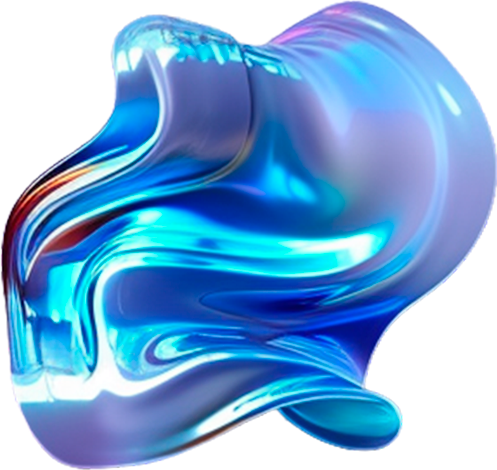
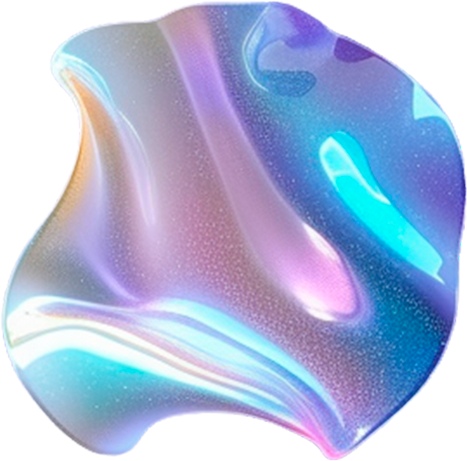
Вячеслав Лукашев отдельно отметил такую проблему пилотного участка, как задержка времени в очередности отгрузки бетона. Также эксперты Регионального центра компетенций обратили внимание на неравномерность загрузки оборудования в течение суток, нестабильную скорость отгрузки разными операторами бетонной установки и неэффективную схему движения транспорта по производственной площадке.
— В ходе совместной работы выявили, что операторы бетонной установки отгружают продукцию с разной скоростью, что не лучшим образом сказывалось на производительности предприятия. Проблема оказалась чисто организационной. Чтобы ее решить, не пришлось перестраивать работу завода, достаточно было разработать стандарт для оператора. Это мы и помогли сделать ООО «ГРОСС ГРУПП ЕК».
Лукашев Вячеслав, руководитель проектов РЦК

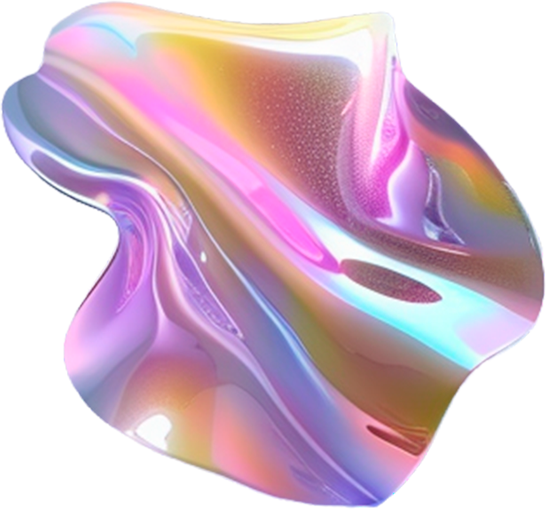
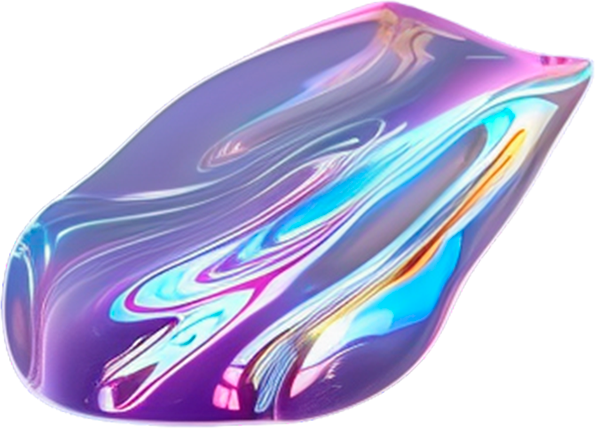
— В моей практике это первый проект в отрасли «Строительство». Совместно с рабочей группой мы достигли необходимых результатов по всем показателям пилотного потока. Увеличили выработку на 30%, снизили объем незавершенного производства на 42% и сократили время протекания процесса на 25%. Мероприятия для достижения необходимых показателей пилотного потока проводили в плановом режиме.
Лукашев Вячеслав, руководитель проектов РЦК
Руководитель проектов РЦК Лукашев Вячеслав отмечает, что в ходе совместной работы сотрудники ООО «ГРОСС ГРУПП ЕК» показали высокую вовлеченность в процесс реализации программы «Производительность труда» на предприятии — от этапа обучения до этапа внедрения.
— Конечно, не обошлось и без сложностей. Основная связана с нехваткой времени на максимальное погружение во все инструменты, ведь теоретические знания нужно воплотить на практике. Поэтому мы старались освобождать рабочее время сотрудников, разгрузить их, чтобы они полноценно могли проникнуться проектом, а также мотивировать, в том числе материально. В этом плане тоже провели большую работу.
Никита Калашников, исполнительный директор ООО «ГРОСС ГРУПП ЕК»
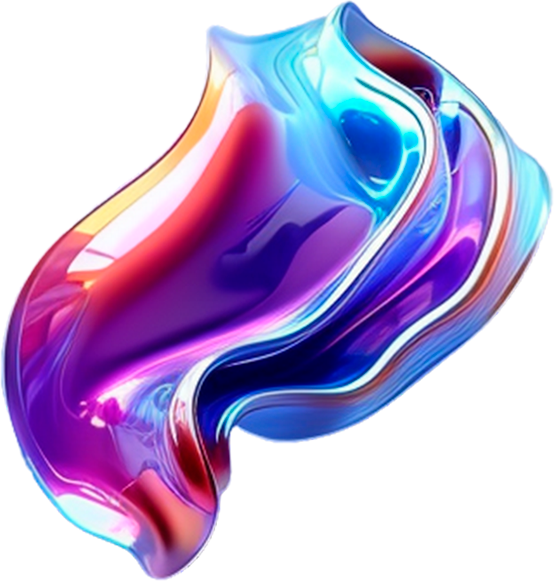
От «Спагетти» до «Автономного обслуживания»
Что помогло сократить задержки в отгрузке бетона
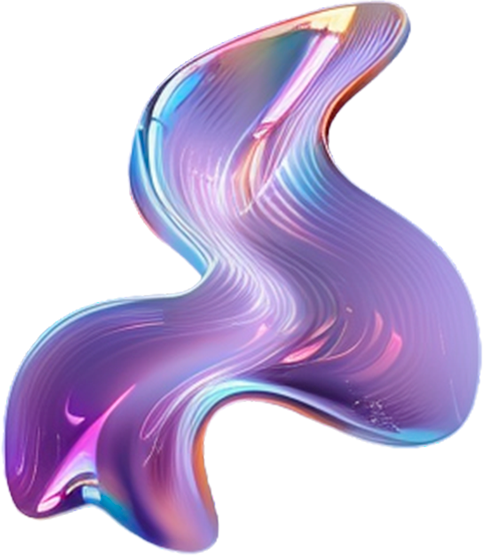