Что это дало
|
«Производительность труда».
Как инструменты бережливого производства помогли единственному
в России предприятию
по выпуску привалковой арматуры
в России предприятию
по выпуску привалковой арматуры
Как производителю оконных систем удалось повысить эффективность труда и запустить сразу несколько новых линий
Как производитель маркерных досок добился снижения потерь и выпуска бракованной продукции
нацпроекта
Губернатор инициировал запуск «младшего брата»
Для того чтобы выйти на новый уровень, заводам не всегда достаточно собственных сил. Поэтому в стране запустили нацпроект «Производительность труда», участвовать в нем могут компании с выручкой от 400 миллионов рублей. Но в поддержке государства нуждаются и небольшие предприятия с меньшим доходом. Поэтому областное правительство утвердило выделение средств из регионального бюджета на внедрение инструментов бережливого производства. Эти деньги помогут предприятиям, которые пока что не могут участвовать в национальном проекте «Производительность труда», инициированном президентом страны.
В 2023 году первые 10 свердловских промпредприятий стали участниками госпрограммы, все они по итогам года улучшили финансовые показатели. В этом году участников уже 20. О том, как проект повлиял на развитие бизнеса, рассказали представители нескольких предприятий.
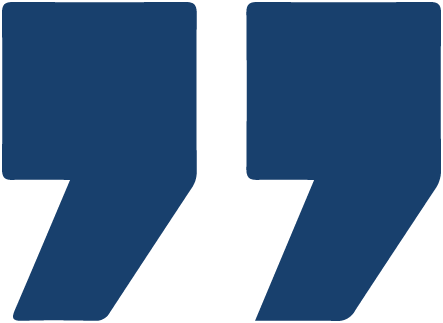
03
02
01
— Благодаря поддержке губернатора Евгения Куйвашева, специалисты Регионального центра компетенций, которые уже имеют колоссальный опыт внедрения инструментов бережливого производства, помогут оптимизировать процессы перспективным компаниям, — сказал министр промышленности и науки Свердловской области Сергей Пересторонин. — Ожидаемый эффект — рост производительности, прибыли, увеличение налогооблагаемой базы и дополнительные отчисления в бюджеты всех уровней.
Следующим 20 компаниям — представителям промпроизводства с выручкой до 400 миллионов рублей — экспертная поддержка будет доступна в следующем году. При этом обозначить желание поучаствовать в региональном проекте можно уже сейчас.
Для участия в национальном проекте «Производительность труда» можно зарегистрироваться на сайте. Заявку рассматривают до пяти рабочих дней.
Для участия в национальном проекте «Производительность труда» можно зарегистрироваться на сайте. Заявку рассматривают до пяти рабочих дней.
адрес: г. Екатеринбург, ул. Конструкторов, 5;
технопарк «Университетский», оф. 2016;
тел.: (343) 227-11-10;
frpso.ru
технопарк «Университетский», оф. 2016;
тел.: (343) 227-11-10;
frpso.ru
03
Ее инновационные магнитные стекло-маркерные доски, а также отделочные материалы и мебель из стекла и керамики украшают офисы «Яндекса», «Сколково», «Сбера», «Москва-Сити», небоскребов в Санкт-Петербурге и других городах России, Казахстана и Белоруссии.
Специалисты Askell первыми в России внедряют новые материалы и архитектурные решения. Так было со стекло-маркерными досками 11 лет назад, а в 2022 году компания освоила керагласс, который раньше можно было заказать только в Италии. Сегодня Askell сконцентрировался на выпуске «умного» стекла: всего одно нажатие на кнопку в телефоне — и остекление перегородки может стать прозрачным или непрозрачным тонированным.
Специалисты Askell первыми в России внедряют новые материалы и архитектурные решения. Так было со стекло-маркерными досками 11 лет назад, а в 2022 году компания освоила керагласс, который раньше можно было заказать только в Италии. Сегодня Askell сконцентрировался на выпуске «умного» стекла: всего одно нажатие на кнопку в телефоне — и остекление перегородки может стать прозрачным или непрозрачным тонированным.
Как производитель маркерных досок добился снижения потерь и выпуска бракованной продукции
Стекло-маркерные доски давно стали незаменимым атрибутом переговорных комнат
в современных офисах. На Урале выпускают и такую продукцию — этим занимается компания Askell.
Ее история берет свое начало со скромного штучного производства маркерных досок для школ и офисов
в Екатеринбурге. Сегодня
у предприятия уже две производственные площадки
с собственным оборудованием, включающим печи, обрабатывающие центры и станки.
в современных офисах. На Урале выпускают и такую продукцию — этим занимается компания Askell.
Ее история берет свое начало со скромного штучного производства маркерных досок для школ и офисов
в Екатеринбурге. Сегодня
у предприятия уже две производственные площадки
с собственным оборудованием, включающим печи, обрабатывающие центры и станки.
Поводом для вступления в программу и внедрения бережливого производства стало наше желание научиться выявлять потери, узнать о методах, позволяющих бороться с потерями, и начать их внедрять, решить вопрос с нехваткой рабочего пространства, а также повысить эффективность труда. Бережливое производство поспособствовало сокращению издержек благодаря оптимизации процессов, улучшению контроля качества продукции и устранению неэффективных действий.
Исполнительный директор Askell Татьяна Бугаева
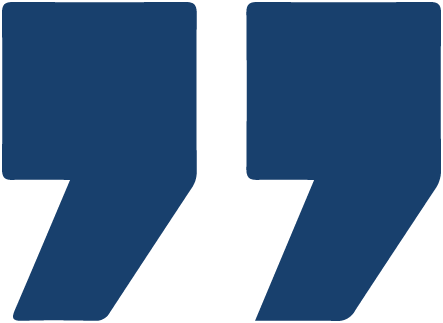
Компания непрерывно растет и развивается. После приобретения в 2020 году собственной производственной площадки по обработке стекла объемы выпуска и продаж продукции выросли примерно в 3,5 раза за 3 года. Сейчас в списке задач к обязательному освоению новых технологий и ниш присоединились переход к бережливому производству и его автоматизация.
Как и в любой другой компании, работу в Askell начали с диагностики — ее провели с особой внимательностью к деталям. Специалисты разработали две карты потоков создания ценности. Одну карту сделали по методологии MIFA — по бизнес-процессу от подачи клиентом заявки до отгрузки готовой продукции. Акцент при этом был именно на взаимодействии между подразделениями.
Параллельно с разработкой карты бизнес-процесса команда выпустила пооперационную карту производственного процесса с более детальным погружением в потери на каждом рабочем месте участков. В результате получили детальный анализ текущего состояния процессов как на производстве, так и в офисе. Результаты такого тщательного анализа легли в основу разработки ключевых решений по оптимизации продуктовых потоков.
Параллельно с разработкой карты бизнес-процесса команда выпустила пооперационную карту производственного процесса с более детальным погружением в потери на каждом рабочем месте участков. В результате получили детальный анализ текущего состояния процессов как на производстве, так и в офисе. Результаты такого тщательного анализа легли в основу разработки ключевых решений по оптимизации продуктовых потоков.
Ощутимый нюанс для конкретного предприятия — это объем номенклатуры производства. Компания очень гибко подходит к желаниям своих клиентов. Так как методология проекта нацелена на оптимизацию одного пилотного потока, выбрать один конкретный продукт не представляется возможным. Однако благодаря команде проекта мы нашли выход из данной ситуации — стали рассматривать производственные операции как один цельный процесс независимо от характеристик отслеживаемого продукта. Такой подход позволил оценить производительность каждой конкретной операции и проблематику на каждом участке для всех продуктов предприятия.
Руководитель проектов РЦК Кирилл Колотков
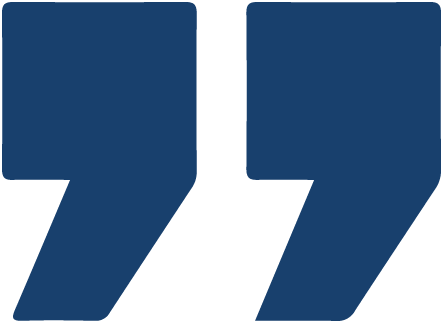
Для внедрения выбрали такие инструменты, как система 5С, «Стандартизированная работа» и «Автономное обслуживание». В совокупности они позволили увеличить производительность на 11,2% и снизить выпуск несоответствующей продукции на 3,1% — с 3,8% до 0,7%.
Стоит отдельно отметить показательное для проектов внедрение системы 5С на двух производственных участках. На самом старте проекта команда провела аудит двух участков и не набрала больше пяти баллов. Но уже после первых недель работы появился интенсивный рост, и улучшения на площадке стали видны невооруженным взглядом. На момент окончания проекта на двух участках специалисты набирали около 20 баллов. Они не ограничились двумя участками и параллельно реализовывали небольшие улучшения на других рабочих местах. А это уже отличный результат.
Стоит отдельно отметить показательное для проектов внедрение системы 5С на двух производственных участках. На самом старте проекта команда провела аудит двух участков и не набрала больше пяти баллов. Но уже после первых недель работы появился интенсивный рост, и улучшения на площадке стали видны невооруженным взглядом. На момент окончания проекта на двух участках специалисты набирали около 20 баллов. Они не ограничились двумя участками и параллельно реализовывали небольшие улучшения на других рабочих местах. А это уже отличный результат.
Поскольку предприятие находится в стадии экстенсивного развития производства, на момент реализации проекта численность команды была небольшой. Но это никак не помешало ей справляться со всеми задачами.
Также мы научились составлять карты информационного потока и производственного цикла, операционные стандарты и стандарты рабочих мест, что позволяет выявлять неэффективные действия и потери, а также стандартизировать работу сотрудников и оборудования для того, чтобы исключить простой оборудования и наличие неэффективных действий команды. Все полученные навыки и внедренные методы бережливого производства стали для нас важными инструментами для прогресса в работе.
Исполнительный директор Askell Татьяна Бугаева
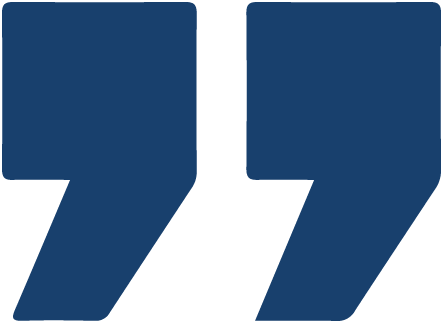
С самого старта проекта мы четко разграничили зоны ответственности каждого участника по внедрению инструментов бережливого производства и систематично достигали поставленных целей. Лично я могу оценить действия команды очень высоко и хочу поблагодарить каждого члена группы за проделанную работу.
Руководитель проектов РЦК Кирилл Колотков
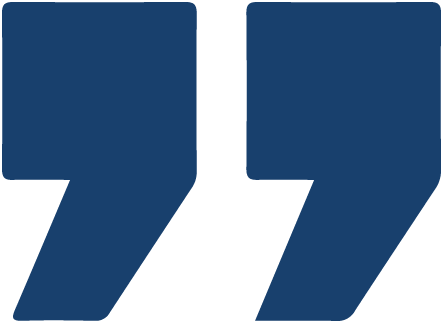
Предприятиям, которые решили вступить в региональный проект, Кирилл Колотков дополнительно рекомендует пользоваться ресурсами и опытом экспертов регионального центра компетенций на полную катушку. Четыре месяца проходят очень быстро, и чем выше новые участники определят приоритет данному проекту, тем выше по итогу будет достигнутый результат.
02
Деревянные окна во многом превосходят пластиковые: они долговечнее, лучше удерживают тепло и поглощают шум. Крупнейшим в УрФО производителем современных оконных систем на основе древесины является группа компаний «ЛесСтройМонтаж». Она работает с 2001 года и также выпускает дерево-алюминиевые окна, пиломатериалы и строганые изделия. Продукцию предприятия приобретают как частные лица, так и компании, в основном это застройщики и домостроительные фирмы по территории всей России.
Как производителю оконных систем удалось повысить эффективность труда и запустить сразу несколько новых линий
Команда «ЛесСтройМонтажа» решила поучаствовать в региональном проекте, чтобы повысить эффективность обработки, оптимизировать производственный процесс, снизить интенсивность труда работников и время протекания складских процессов, получить новые профессиональные компетенции. Сотрудникам компании необходимо было научиться видеть проблемы и организовывать системы их решения.
Передо мной стояла задача передать предприятию методы ведения проектов и умение пользоваться инструментами бережливого производства, чтобы в дальнейшем компания могла самостоятельно реализовывать аналогичные проекты и продолжать повышать производительность труда. «ЛесСтройМонтаж» — это предприятие практически полного цикла с очень длинной производственной цепочкой. Работа начинается с распила кругляка (необработанного ствола дерева), самостоятельной сушки досок и клейки из них бруса, затем идет изготовление деталей для окон. Мы с коллегами решили взять для оптимизации процесс этапа заготовки бруса. Это позволило повысить эффективность работы участников и проекта в целом.
Руководитель проектов РЦК Василий Силин
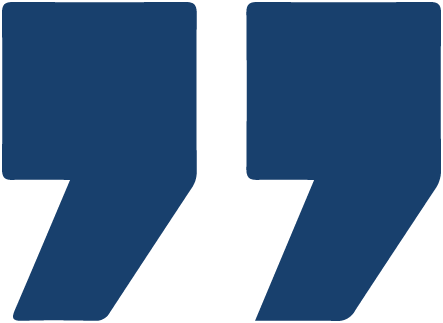
Во время участия в проекте на предприятии произошли позитивные перемены: здесь запустили три линии лесопиления и запустили участок выпуска погонажных изделий, а также провели модернизацию участка производства бруса.
В качестве эталонного изделия решили выбрать окно «Евро 78 15-21». Проанализировав производственный поток, на предприятии выделили три основных недочета: большое количество лишних транспортировок и перемещений, частые остановки линии на замену мешков с опилом и переналадки, недостаток квалифицированного персонала.
В качестве эталонного изделия решили выбрать окно «Евро 78 15-21». Проанализировав производственный поток, на предприятии выделили три основных недочета: большое количество лишних транспортировок и перемещений, частые остановки линии на замену мешков с опилом и переналадки, недостаток квалифицированного персонала.
Мы берем курс на увеличение мощностей. Это касается направления производства пиломатериалов и деревянных окон. Раньше у нас была одна линия лесопиления, сейчас их три. А на участке заготовке оконных блоков появилось новое оборудование. Также сейчас реализуем проект по модернизации участка покраски конструкций. А в рамках регионального проекта у нас проходят мероприятия, направленные на снижение потерь — так мы повысим производительность труда и снизим трудоемкость.
Руководитель проектного офиса «ЛесСтройМонтаж» Ульяна Юшкова
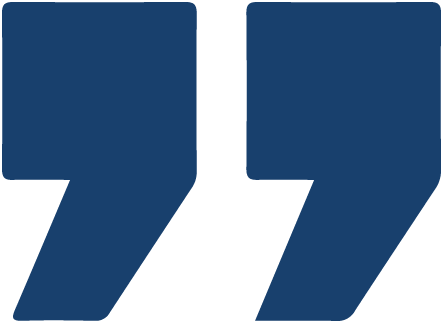
Поэтому основными направлениями оптимизации обозначили стандартизацию и оптимизацию времени переналадки, внедрение матрицы компетенций, обучение персонала на ее основе для обеспечения полной взаимозаменяемости, разработку стандартов для рабочих и технических решений в целях уменьшения времени на транспортировку отходов производства.
В исполнении этих задач помогли инструменты бережливого производства: 5C, SMED, «Стандартизированная работа», «Матрица компетенций». Кроме этого, «ЛесСтройМонтаж» подробно рассмотрел свои бизнес-процессы при помощи инструмента «Картирование офисных процессов» и уже готовит изменения в своей ERP-системе для оптимизации процессов для всего сектора B2В.
В исполнении этих задач помогли инструменты бережливого производства: 5C, SMED, «Стандартизированная работа», «Матрица компетенций». Кроме этого, «ЛесСтройМонтаж» подробно рассмотрел свои бизнес-процессы при помощи инструмента «Картирование офисных процессов» и уже готовит изменения в своей ERP-системе для оптимизации процессов для всего сектора B2В.
Василий Силин отмечает и другие плюсы участия в проекте. Сотрудники компании увидели потери, простои на участках, проблемы производственного потока и выявили узкие места. На основе этого разработали технические решения, которые позволили существенно расширить так называемое бутылочное горлышко. Хорошо помог инструмент «Матрица компетенций»: он показал неравномерность навыков бригад, работающих на одном участке в разные смены и выдающих непостоянную эффективность.
На опытном участке с помощью инструмента 5С мы оптимизировали уборку отходов. Если раньше сортировка шла вручную, то сейчас есть автоматический конвейер, по которому отходы самостоятельно утилизируются и складируются на улице. У нас сократилось время на замену мешков, вынос мусора и передвижения на транспорте. Кроме того, мы запускаем процесс обучения сотрудников, чтобы сделать их мультифункциональными, обеспечить взаимозаменяемость на разных участках и операциях. Для этого также в планах стоит стандартизация операций на различных станках на опытном участке.
Руководитель проектного офиса «ЛесСтройМонтаж» Ульяна Юшкова
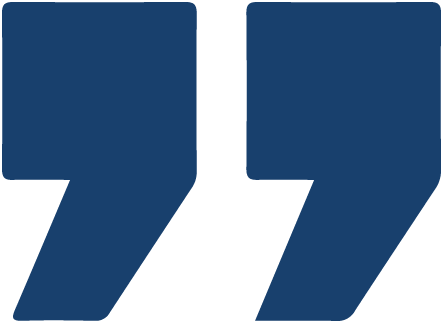
Помимо этого, в процессе реализации находится инструмент «Стандартизированная работа». Команда предприятия планирует стандартизировать основные операции на участке заготовки, чтобы каждый сотрудник мог работать с одинаковой эффективностью. К тому же это позволит серьезно сократить период обучения и адаптации новых специалистов, что в условиях общего кадрового голода чрезвычайно важно.
На предприятии работает слаженная команда профессионалов. Руководство компании постоянно занимается обучением своих сотрудников, поэтому им было легко влиться в новые процессы и работать над проектом. Тем, кто только входит в проект, нужно помнить, что за большими результатами стоит кропотливая работа целой команды.
Руководитель проектов РЦК Василий Силин
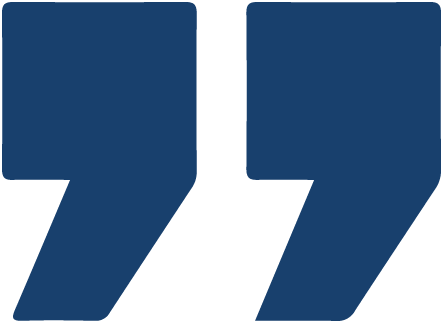
Сейчас на рынке труда заметный дефицит кадров, поэтому предприятиям необходимо принимать меры, чтобы удержать действующих сотрудников, облегчить им работу и повысить производительность с уже имеющимися ресурсами.
01
Завершает участие в региональном проекте «Производительность труда» сейчас компания «Гайд Системс» — первая и единственная в России, профессионально занимающаяся привалковой арматурой и процессами прокатки. Уже 8 лет предприятие специализируется на изготовлении металлургического оборудования и запчастей по чертежам заказчика на высококлассном оборудовании Okuma. Ручной труд минимизировали, чтобы обеспечить высокое качество продукции.
Как инструменты бережливого производства помогли единственному в России предприятию по выпуску привалковой арматуры
Клиентами компании являются такие гиганты промышленности, как SMS Group, ЕВРАЗ, АЭМЗ, «Уралмаш», «Русал», «Сибур», «Северсталь», НЛМК. География поставок продукции включает всю территорию России, а также Казахстана, Узбекистана и Беларуси. Входя в проект, команда «Гайд Системс» ставила перед собой задачу сбалансировать все потоки, повысить производительность труда и снизить потери, ведь впереди у компании строительство новых мощностей.
Любой процесс состоит из повторяющихся действий — а значит, его можно оптимизировать. В этом мы рассчитываем на совместную работу с командой экспертов регпроекта. Мы понимаем, что внедрение бережливого производства требует вовлеченности всех наших сотрудников и, как следствие, их мотивации. Для этого мы участвуем в данном проекте — хотим повысить качество работы за счет сокращения потерь и затрат производства, что во многом зависит от взаимодействия всего персонала.
Директор «Гайд Системс» Александр Сторожков
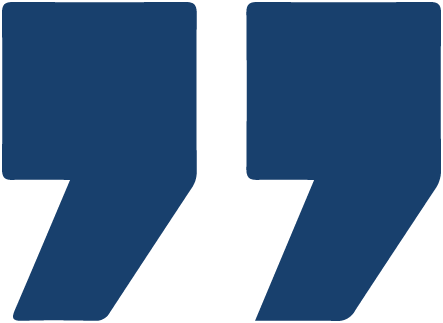
В первую очередь в «Гайд Системс» сосредоточили внимание на оптимизации процесса производства корпуса подшипника МНЛЗ. К середине проекта удалось выявить несколько проблем: длительное время переналадки, частые остановки станка от вибрации по ошибке, а также сокрытие аварийных остановок и их причин.
Чтобы оптимизировать процесс, понадобилось ввести новые стандарты, изменить время переналадки и технологию производства детали, сформировать базу знаний по рабочим процессам в формате видеороликов, уроков по одной теме и создать план производства с учетом фактической сложности работ. Также на предприятии внедрили инструменты бережливого производства: 5C, SMED, «5 почему», «Стандартизированная работа», «Производственный анализ».
В целом предприятие выбрало курс на совершенствование системы планирования и подготовки производства, внедрение регламентов и стандартов.
Чтобы оптимизировать процесс, понадобилось ввести новые стандарты, изменить время переналадки и технологию производства детали, сформировать базу знаний по рабочим процессам в формате видеороликов, уроков по одной теме и создать план производства с учетом фактической сложности работ. Также на предприятии внедрили инструменты бережливого производства: 5C, SMED, «5 почему», «Стандартизированная работа», «Производственный анализ».
В целом предприятие выбрало курс на совершенствование системы планирования и подготовки производства, внедрение регламентов и стандартов.
— В целом команда — огонь, очень современная и смелая, с большими запросами и целью «захватить мир». Когда я приходила к ним на производство, они всегда старались меня удивить. Новую информацию во время тренинга тут же пытаются воплотить теми подручными способами, которые у них есть. Все новшества не откладывают в долгий ящик, сразу же применяют в деле, поэтому быстро понимают, заходит им инструмент или нет, — рассказала руководитель проектов «Регионального центра компетенций» Мария Делягина. — Поэтому тем, кто только подключается к проекту, я советую качественно подойти к выбору команды, а также собрать больше сведений о проблемах, с которыми приходится сталкиваться в работе.
Корпуса подшипников МНЛЗ — это самый трудозатратный продукт с большим количеством операций, именно поэтому нужно было по максимуму убрать потери, чтобы выпускать больше продукции с теми же ресурсами. Мы сконцентрировались на этой задаче и попутно провели опрос, выяснив, можно ли реализовать инструменты бережливого производства на всем предприятии. Компания небольшая, площадь цеха — порядка 400 квадратных метров. Мы начали внедрять инструменты, которые подразумевает проект, на эталонных местах возле фрезерных станков, далее перешли на токарные станки и постепенно привели в порядок всю рабочую зону. Сейчас в компании рассчитывают экономический эффект, но уже можно сказать, что время протекания процесса — а это один из показателей, который мониторится в проекте, — стало меньше и производительность труда по выпуску основного изделия повысилась.
Руководитель проектов «Регионального центра компетенций» Мария Делягина
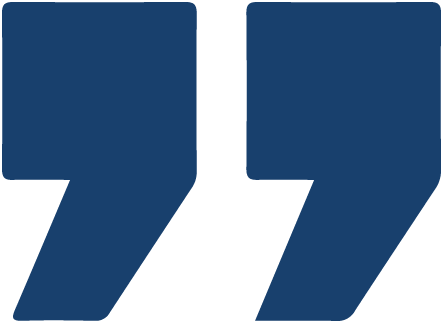
По словам директора по развитию «Гайд Системс» Дмитрия Мулинова, команде стало интересно испытать на себе инструменты бережливого производства, поработать с цифрами и производительностью труда. Такой показатель на предприятии вели еще до проекта и, конечно, хотели бы на него влиять.
Проект разделен на две фазы. Первая — это теоретическая подготовка. Мы изучаем, какие инструменты есть, какие мы могли бы применить у себя — сначала в игровой практике, затем в реальных процессах. Мозговые штурмы в командных играх позволили нам найти технологическое преимущество и воспользоваться им. Через две недели удалось снизить аварийный простой оборудования. Мы получили реальный эффект за счет всего лишь одного инструмента. Поэтому в дальнейшем отношение команды к другим инструментам бережливого производства изменилось, и теперь мы применяем их ежедневно.
Директор по развитию «Гайд Системс» Дмитрий Мулинов
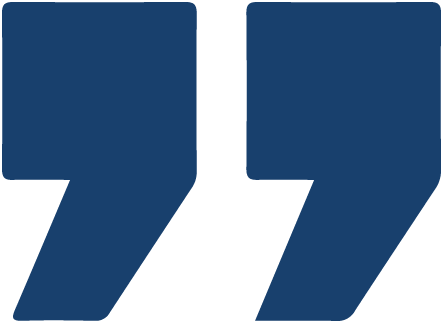
Компания «Гайд Системс» не планирует останавливаться на участии в региональном проекте. В будущем на предприятии хотят закрепить успех и поучаствовать в национальном проекте «Производительность труда». Тогда в работу можно будет взять не какой-то один продукт,
а весь производственный процесс в целом.
а весь производственный процесс в целом.