Большая перезагрузка
Вдохновляющие истории предприятий, которые решились на преобразования и совершили качественный скачок
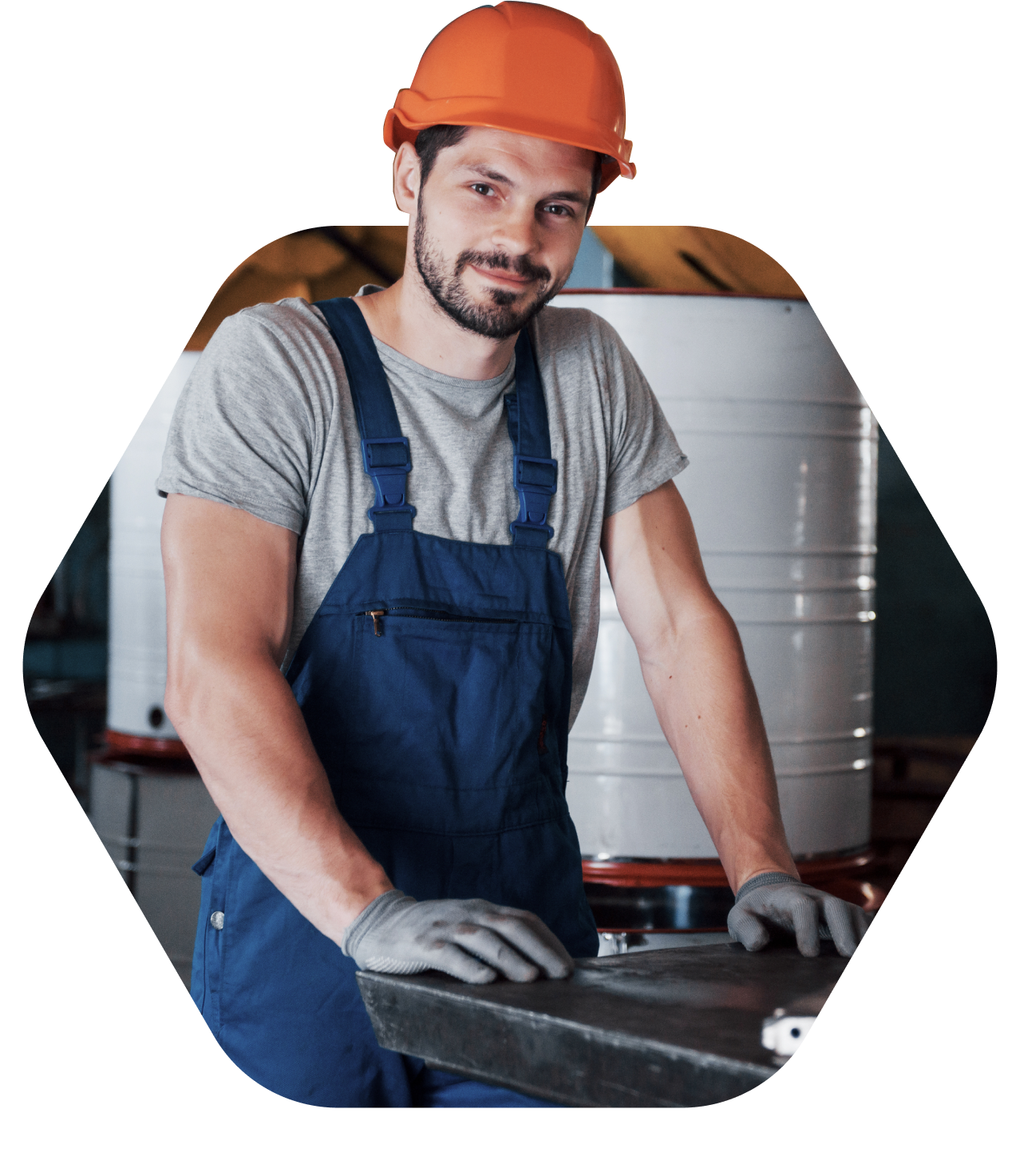
Вот уже пять лет по Свердловской области шагает нацпроект «Производительность труда». За это время к нему присоединились более 250 компаний из самых разных отраслей промышленности. За эти годы множество предприятий добились блестящих результатов. Их положительный опыт вдохновляет других так же идти по пути оптимизации и качественных перемен.
Вместе с Региональным центром компетенций в сфере производительности труда, являющимся оператором проекта в регионе, мы собрали самые яркие кейсы последнего года.
Вместе с Региональным центром компетенций в сфере производительности труда, являющимся оператором проекта в регионе, мы собрали самые яркие кейсы последнего года.
Благодаря продукции заводов — героев этой публикации строятся новые здания, на дорогах и в городах светло, полки магазинов полны продуктов, а в домах уральцев тепло и уютно.
— В недавнем послании Федеральному собранию президент четко обозначил проблемы, которые сегодня стоят перед страной, и способы их решить. Если мы хотим преодолеть кадровый дефицит и повысить эффективность отечественной промышленности, нам критически важно кардинально поднять производительность труда. Поэтому нацпроект планируют продлить до 2030 года. Но пока будущие параметры и цели проекта не утверждены, госпрограмма действует до конца 2024 года. Если предприятие хочет присоединиться к ней в ее текущей конфигурации, оно может сделать это в течение ближайшего месяца — и уже в этом году получить государственную поддержку.
Александр Казаков, генеральный директор Фонда технологического развития промышленности Свердловской области
Нацпроект стартовал в 2018 году с целью поднять производительность труда отечественных компаний минимум на 15%. По данным Фонда развития промышленности Свердловской области, благодаря нацпроекту эффективность оптимизированных участков выросла в среднем в полтора раза, а время изготовления продукции сократилось на 40%. Выявленный экономический эффект уже превысил 3 миллиарда рублей.
Реализацией госпрограммы на территории Свердловской области занимается Региональный центр компетенций в сфере производительности труда Свердловской области (РЦК). Согласно опросу РЦК, 92% предприятий, участвовавших в проекте, удовлетворены результатами.
Реализацией госпрограммы на территории Свердловской области занимается Региональный центр компетенций в сфере производительности труда Свердловской области (РЦК). Согласно опросу РЦК, 92% предприятий, участвовавших в проекте, удовлетворены результатами.
Как прокачивают уральские предприятия
В проекте принимают участия малые, средние и крупные предприятия из самых разных отраслей: промышленность, строительство, сельское хозяйство, транспорт, торговля, логистика и другие. В 2024 году стало известно, что нацпроект «Производительность труда» расширили на туристическую отрасль. Теперь предприятия сферы туризма с выручкой от 180 миллионов рублей теперь могут воспользоваться экспертной поддержкой федерального и сети региональных центров компетенций в сфере производительности труда.
Кто может принять участие в проекте
Как бережливое производство помогло наукоемкому предприятию справиться со взрывным спросом
01
02
Как «упаковали» завод по производству упаковочных машин и дозаторов
Как флагман российского металлостроения всего за три месяца увеличил выработку на одном из участков на 58%
03
04
Как предприятие, которое делает города светлее, повысило производительность, просто переставив станки
Блестящий результат группы компаний «Прософт-Системы» в нацпроекте «Производительность труда» — пример того, как суперсовременная и технологичная компания использует свои резервы и возможности для дополнительного роста.
как бережливое производство помогло наукоемкому предприятию справиться со взрывным спросом
— В 2023 году у нас был взрывной рост заказов. И нам потребовались новые методики, чтобы отрабатывать такое количество заявок. Для этого нужно было достаточно серьезно нарастить объём выпускаемой продукции. Еще до начала проекта мы начали это делать: внедрили у себя на предприятии конвейерную сборку программируемых логических контроллеров. Наша задача состояла в том, чтобы грамотно организовать производство и получить максимум производительности от конвейера.
Роман Туканов, начальник конструкторско-технологического отдела «Прософт-Системы»
Группа компаний «Прософт-Системы» с 1995 года занимается разработкой и внедрением под ключ высокотехнологичных приборов и систем автоматизации. Оборудование этой компании используется буквально везде, где нужна автоматизация процессов, будь это автоматический розлив напитков на пищевом производстве или управление сложной турбиной на ГЭС.
Сильнейшая команда — инженеры, конструкторы и программисты — создают сложную электронику, сами разрабатывают софт и внедряют автоматизированные системы под ключ на самые разные промышленные объекты. Так они помогают предприятиям любых отраслей быть технологичными и современными. Большая доля заказов приходится на нефтегазовый сектор и энергетику, стратегически важные для всей страны.
К автоматизации сегодня стремятся все предприятия, которые хотят идти в ногу со временем, поэтому продукция ГК «Прософт-Системы» становится всё более востребованной.
В условиях постоянно растущего спроса компания внедряет новые способы повышения производительности труда. Участие в нацпроекте позволило им взглянуть на свое производство глазами экспертов РЦК и сделать стремительный рывок вперед.
Эксперт по автоматизации
В качестве эталонного выбрали участок конвейерной сборки программируемых логических контроллеров. Именно эти устройства помогают автоматизировать любые технологические процессы и являются ключевой частью комплексных решений по автоматизации.
Результат не заставил себя ждать
— У нас не бывает одинаковых проектов, но тот, что мы реализовали на предприятии «Прософт-Системы», был, наверное, самым неклассическим. Это предприятие с очень высоким уровнем развития, у них внедрено уже очень много интересных решений. Еще один плюс ребят из «Прософт-Систем» — очень крутые компетенции. У них изначально собраны сильные специалисты, которые на любое мое предложение улучшить что-то не говорят: «У нас всегда так было, мы не будем ничего менять», а наоборот начинают генерировать идеи, как мою рекомендацию можно применить конкретно на их производстве.
Алексей Кувалдин, старший руководитель проектов Регионального центра компетенций в сфере производительности труда
На участке провели перебалансировку нагрузок, перераспределили задачи и определили, что конвейер с тем же составом операторов может производить на 30% контроллеров больше. Так, в ноябре 2023 года, когда компания «Прософт-Системы» только заходила в проект, данный конвейер выпускал порядка 15 тысяч модулей в месяц. На текущий момент, спустя всего 4 месяца, этот показатель составляет 23 тысячи.
С помощью экспертов Регионального центра компетенций удалось детально оценить весь производственный процесс от начала и до конца — с момента получения комплектующих на склад до отгрузки готовой продукции. Грамотный анализ производственного потока помог выявить узкие места, оптимизировать процессы и заметно повысить выработку без каких-либо финансовых вложений.
Еще одним результатом проекта стало появление проектного офиса на предприятии, который будет отвечать за масштабирование методик и техник бережливого производства на другие производственные участки.
Кто достигает большего успеха в проекте
— У нас есть комплексный план мер для достижения целевых показателей, который мы сейчас выполняем. И мы идем к своему идеалу. Общее впечатление от проекта у нас очень положительное. Нам передали важные методики, и мы можем работать не вслепую, а опираться на большой опыт команды РЦК. Мы остались довольны этим сотрудничеством: они выстроили очень грамотную работу, очень хорошо провели обучение и глубоко погрузились в наши процессы.
Роман Туканов, начальник конструкторско-технологического отдела ГК «Прософт-Системы»
Работа специалистов Регионального центра компетенций на предприятиях предполагает тесное взаимодействие с коллективом, в том числе обучающие мероприятия. Тренинги включают мини-лекции и практические задания, чтобы сотрудники могли сразу применять полученные знания у себя на производстве и искать решение проблем.
— Нас часто спрашивают, почему одни предприятия добиваются больших успехов в проекте, чем другие. Результаты во многом зависят от вовлеченности команды, руководства в процесс. Понятно, что компетенции важны, но еще большее влияние оказывает всеобщее понимание коллектива, что им всем это действительно нужно. Тогда скорость движения кратно возрастает. Тем, кто тоже войдет в проект, я бы посоветовал в деятельности по оптимизации совместить две цели. Во-первых, конечно, сделать лучше для предприятия. Во-вторых, получать удовольствие от самого процесса и относиться к переменам как к решению сложных, интересных задач, квесту, который надо пройти и победить.
Алексей Кувалдин, старший руководитель проектов Регионального центра компетенций в сфере производительности труда
Когда в супермаркете вы набираете корзину продуктов, можете быть уверены: там точно есть товары, которые упаковали с помощью оборудования компании «Сигнал-Пак».
как «упаковали» завод по производству упаковочных машин и дозаторов
«Сигнал-Пак» уже 34 года производит в Екатеринбурге технологические и упаковочные аппараты для пищевой промышленности. Среди его клиентов известные мясокомбинаты, предприятия агропромышленного комплекса, кондитерские фабрики: «Макфа», «Белая дача», «Мираторг», «Экомилк» и многие другие.
Производитель является разработчиком уникальных машин для пищевой отрасли и общественного питания. Здесь гордятся уникальной линией по фасовке муки в бумажные пакеты и линией по упаковке зернистого творога. В настоящий момент на молочных предприятиях России и странах СНГ действуют более 100 таких «творожных» линий. И по данным «Сигнал-Пак», 9 из 10 пакетов с творогом, которые вы видите в магазинах, получены на оборудовании уральского предприятия.
Предприятие с именем и историей
В ассортименте компании 20 моделей упаковочных машин и дозаторы для любых типов продуктов, оборудование для производства полуфабрикатов; линии по упаковке в бумажный пакет, брикетёры; системы охлаждения и заморозки; линейки оборудования по сушке, калибровке, мойке и фасовке овощей; транспортирующие системы. В общем всё, благодаря чему пищевая отрасль может обеспечивать людей продуктами питания.
«Сигнал-Пак» вошел в проект «Производительность труда» в августе 2023 года. Окончательное решение об участии в проекте руководители приняли после экскурсии на одно из предприятий, которое уже оптимизировало производство вместе со специалистами Регионального центра компетенций.
Как завод попал в проект
— Наше предприятие имеет очень широкий ассортимент изготавливаемого оборудования, и поначалу мы сомневались: будут ли у нас так же эффективны инструменты бережливого производства, как на заводах, специализирующихся на серийном производстве. Мы съездили на предприятие КМЗ в Артёмовский, у которых тоже большая номенклатура, и нам очень понравилось. У руководства глаза горели, они много нам рассказали, показали, что поменяли, что переделали, и очень восторженно отзывались о проекте. Поэтому сомнений у нас не осталось.
Егор Швец, исполнительный директор «Сигнал-Пак»
С конца 2022 года на предприятие «Сигнал-Пак» пошел очень большой поток заказов. Европейские производители ушли с рынка, и крупные компании пищевой отрасли, аграрного сектора обратили свое внимание на отечественных производителей.
— Когда крупные заказчики стали приезжать к нам на площадку и увидели, какое мы делаем оборудование, они были приятно удивлены. Такой интерес, конечно, тоже послужил для нас стимулом к развитию. Мы выбрали пельменные автоматы, потому что это наиболее технологичное оборудование в нашей линейке. Обилие сложных поверхностей и длительных технологических цепочек изготовления в совокупности давало длительный цикл производства. И наша задача была минимизировать сроки производства, чтобы обеспечить российскую пищевую отрасль современным оборудованием.
Егор Швец, исполнительный директор
Чтобы удовлетворить возросший спрос, было решено оптимизировать технологию изготовления, и инструменты бережливого производства оказались как раз кстати.
В качестве пилотного потока выбрали пельменные аппараты. Впервые такой агрегат разработали в 2007 году, и он оказался очень востребованным не только в России, но и во многих других странах. Егор Швец, будучи молодым специалистом, 15 лет назад тоже участвовал в создании первого пельменного аппарата.
Пилотный проект —пельменные аппараты
— Коллектив ВКП «Сигнал-Пак» крайне быстро включился в процесс улучшений. С самого старта проекта, после первых тренингов, команда проекта начала реализовывать первые мероприятия. Руководители активно участвовали практически в каждом совещании рабочей группы, принимали решения, брали на себя ответственность за мероприятия. В начале проекта было понятно, что только с таким темпом и вовлеченностью, на мой взгляд, можно было достичь конкретных результатов.
Кирилл Колотков, руководитель проектов Регионального центра компетенций в сфере производительности труда
В итоге результаты совместной работы проектной команды «Сигнал-Пак» и специалистов РЦК оказались просто блестящими. На текущий момент трудоемкость процесса удалось снизить на 24%, эти цифры еще подрастут. Яркий пример оптимизации: только из-за увеличения жесткости корпуса удалось повысить скорость обработки на фрезерном обрабатывающем центре почти в 1,5 раза. Еще одно впечатляющее достижение — время пролеживания с 72 дней сократилось до 29 за счет оптимизации технологической цепочки и логистики. На предприятии сообщили, что портфель заказов пельменного оборудования в этом году уже значительно вырос — на 23 % по сравнению с показателями прошлого года.
Руководители «Сигнал-Пака» планируют по окончании проекта развивать полученный успех и применять полученные знания на другом оборудовании. В ближайших планах — оптимизация производства упаковочных машин и комбинационных дозаторов. Это тоже очень востребованная продукция.
У предприятия новые цели
Теперь в планах предприятия — строительство нового производственного корпуса на 1500 квадратных метров. Новые задачи требуют и новых квалифицированных кадров.
Проект «Производительность труда» помог «Сигнал-Паку» взять курс на дальнейшие качественные преобразования, а значит, сотрудников ждут стабильность и профессиональный рост, а предприятие — новые высоты и достижения.
— На мой взгляд, значимые результаты принесли следующие инструменты: картирование, диаграмма «Спагетти», 5С. Картирование позволило команде проекта под другим углом взглянуть на процесс изготовления оборудования, пересмотреть технологичность определенных узлов и деталей, разобраться в информационном потоке. В ходе составления диаграммы «Спагетти» было выявлено определенное количество петель при перемещении продукции в цехах. Часть из них была ликвидирована пересмотром технологического процесса производства. Часть — переносом склада сырья и материалов. Система 5С — базовый инструмент бережливого производства, который стал внедряться практически со старта проекта.
Кирилл Колотков, руководитель проектов Регионального центра компетенций в сфере производительности труда
В настоящий момент «Сигнал-Пак» ведет набор сотрудников на рабочие специальности: фрезеровщик, токарь, оператор станков с ЧПУ, слесарь — сборщик металлоконструкций. А в отдел разработки требуются талантливые программисты и инженеры-конструкторы.
На заводе очень дружный коллектив и хорошие условия труда. Более 60% сотрудников работают более 10 лет на предприятии и около 20% — более 15 лет.
Более трехсот лет нижнетагильский металл известен во всём мире. С демидовских времен он является синонимом надежности и качества. Нижнетагильский завод металлических конструкций подтверждает эту славу и в настоящее время.
как флагман российского металлостроения всего за три месяца увеличил выработку на одном из участков на 58%
— На старте проекта основными задачами мы видели снижение времени протекания процесса, сокращение незавершенного производства и увеличение выработки на одного человека. Ранее мы самостоятельно занимались оптимизацией производственной системы, но при адресной поддержке сотрудников РЦК работа проводилась в другом формате, что позволило нам увидеть проблемы с другой стороны, так как в процессе были задействованы сотрудники, которые ранее не имели ни опыта, ни возможности участия в работе по данному направлению. В состав рабочей группы вошли сотрудники из числа рабочих и инженерно-технического персонала, которые прошли обучение по основам бережливого производства, реализации проекта по улучшениям, картированию, системе 5С на производстве.
Николай Золотарев, главный инженер НТЗМК
ООО «НТЗМК» производит металлоконструкции на Урале уже более 80 лет. Предприятие входит в число крупнейших производителей металлоконструкций в России. За его плечами полное ярких достижений прошлое и перспективное настоящее.
Производитель занимается выпуском строительных стальных металлоконструкций для самых разных объектов промышленного, гражданского и специального назначения. Продукция НТЗМК использовалась для строительства олимпийских объектов в Сочи, аэропорта Пулково и Лахта-центра в Санкт-Петербурге, МВЦ в Екатеринбурге и космодрома «Восточный» в Амурской области. Среди заказчиков компании — промышленные гиганты со всей России: ЕВРАЗ, «Сибур», НЛМК, «Норникель», УГМК и другие.
Чтобы реализовывать крупные проекты, соответствовать требованиям времени и повышать свою конкурентоспособность на рынке, руководители НТЗМК приняли решение поучаствовать в нацпроекте «Производительность труда». Для предприятия такого масштаба преобразования — это не только возможность оптимизировать производство, но и повысить уровень жизни и благосостояние своих сотрудников.
Промышленный гигант открыт переменам
Особенность проекта — масштаб изделий
В качестве эталонного выбрали один из участков цеха металлоконструкций, где происходит сборка и сварка конструкций. Данный участок является универсальным, и на его базе происходит изготовление конструкций любых типов и сложности. Для детального анализа взяли конкретный производственный поток — изготовление конструкций уникального сооружения для Новокузнецкого металлургического комбината. Процесс разобрали на составляющие, чтобы выявить, где происходят потери.
— Основная особенность данного проекта — масштаб выбранного изделия. Я думаю, вытяжная башня — это один из самых крупных продуктов, который мы брали в проект в РЦК. Было интересно увидеть, как будет работать бережливое производство на таком предприятии. Основная сложность была в хронометраже такого гигантского изделия, ведь подобные конструкции не делаются быстро. Мы разбили хронометраж на несколько этапов и поочередно с ними работали, прорабатывали проблемы и мероприятия по их устранению. Очень приятные впечатления остались от работы с коллегами на НТЗМК. Они занимаются изготовлением очень серьезных объектов из металлоконструкций и с такой же серьезностью подошли к проекту. Каждый человек в рабочей группе — настоящий профессионал своего дела, для которого нет непреодолимых трудностей и задач.
Василий Силин, руководитель проектов Регионального центра компетенций в сфере производительности труда
В данный момент НТЗМК находится в стадии внедрения разработанного плана мероприятий и подведения промежуточных итогов. Положительные результаты уже есть.
Предварительные результаты впечатляют
Например, в ходе проекта на предприятии выполнили перепланировку одного из участков, сократив используемые площади практически в два раза — с 3029 до 1616 квадратных метров. Благодаря производственному анализу, оптимизации технологии изготовления и логистики удалось повысить производительность на 58% и увеличить выработку на одного работника с 3,3 тонны до 5,5 тонны.
— Однозначно весь положительный опыт, полученный в рамках реализации данного проекта, мы планируем масштабировать на всё предприятие. На заводе был создан проектный офис, и инструменты, которым нас обучили сотрудники РЦК, мы будем использовать в своей деятельности, адаптировав под необходимые задачи. Кроме того, у нас запущена программа рационализаторства, в рамках которой уже есть внедренные предложения. За все поданные предложения предполагаются поощрительные выплаты, а по итогам квартала мы будем выбирать три лучших инициативы.
Константин Бишаров, ведущий инженер-технолог по сопровождению заказов
Не секрет, что чем масштабнее и старше предприятие, тем сложнее его коллективу менять установки, которые десятилетиями формировались на производстве. Проект «Производительность труда» стал для НТЗМК возможностью объединить сотрудников и показать им, что путь преобразований и улучшений — это благо не только для предприятия, но и для них самих.
Как коллектив включился в процесс
— Сопротивление изменениям у некоторых сотрудников было, но большая часть команды проекта зарядилась новыми идеями, поверила в то, что в силах менять действительность в лучшую сторону. Важную роль в мотивации работников сыграла поддержка специалистов РЦК. Помимо высокого уровня компетенций в предметных областях проекта, коллеги из РЦК демонстрировали спартанскую выдержку, здоровый оптимизм и несгибаемость на пути к цели. Они добивались понимания материала, вникали в суть проблем, задавали наводящие вопросы, как настоящие тренеры, заставляя команду самостоятельно мыслить, изобретать, анализировать. С помощью специалистов РЦК мы смогли по-новому взглянуть на многие процессы.
Александра Гринькова, директор по персоналу и социальной политике
Качественное освещение помогает снизить на трассах аварийность, а на предприятиях — травматизм, делает улицы и дворы безопаснее. Вот уже 16 лет освещает города, дороги и заводы России производственно-торговое предприятие «Энерго-Арсенал».
как предприятие, которое делает города светлее, увеличило выработку, просто переставив станки
Уральское предприятие «Энерго-Арсенал» делает светлее города, поселки, трассы и заводы по всей России — от Мурманска до Дальнего Востока.
Оно специализируется на создании комплексных линий освещения для государственных и коммерческих заказчиков и производит осветительные приборы под собственными торговыми марками: граненые и трубчатые опоры, уличные и промышленные светильники.
Эксперт по освещению
«Энерго-Арсенал» участвовал в освещении крупных автодорог, таких как Москва — Казань, Казань — Екатеринбург. Когда с помощью продукции предприятия осветили часть объездной дороги Липецка, аварийность на этом участке сразу снизилась на 85%. В данный момент «Энерго-Арсенал» подписал контракт на освещение трассы Екатеринбург — Пермь.
Инженеры и программисты компании разрабатывают передовые автоматизированные системы освещения, которые уже сейчас востребованы в крупных компаниях. Они позволяют управлять освещением удаленно с телефона, регулировать яркость и другие параметры и экономить энергоресурсы, снижая затраты на эгнергопотребление от 30 до 80%
Как предприятие вошло в проект
Главные составляющие линий освещения — граненые опоры. Это стальные столбы, на которых размещается светильник с питающим кабелем. Требования к такой продукции очень высокие: она должна выдерживать сильные нагрузки и различные погодные условия — ураганный ветер, снежный шторм, обледенение. Изготовление опор требует больших производственных помещений.
— Чтобы войти в проект, необходимо, чтобы годовая выручка предприятия составляла минимум 400 миллионов рублей. Как только мы преодолели этот показатель, сразу подали заявку на участие. Одна из ключевых целей, которую мы озвучили специалистам РЦК, — это повысить производительность на ограниченных производственных пространствах. И они с ней блестяще справились.
Дмитрий Вострецов, генеральный директор предприятия «Энерго-Арсенал»
Граненые опоры освещения — важная часть портфеля заказов предприятия. В 2023 году доля выручки по данным изделиям составила 30% от общего объема продукции.
Карта идеального состояния потока
Взглянуть на производственный процесс граненых опор со стороны собрались сотрудники офиса, непосредственно производственники и специалисты Регионального центра компетенций. Вместе они разработали карту идеального состояния производственного потока, при котором он движется без задержек и потерь.
— В этом проекте нам удалось очень эффективно поработать с инструментом стандартизированной работы, и именно он дал наибольший результат. Мы детально разобрали одну из ключевых операций и посмотрели, какие элементы работы усложняют и увеличивают ее время. При анализе уже проведенных хронометражей выявили потери, связанные с излишней обработкой на операции и с лишней транспортировкой. Исходя из анализа, принимались решения по устранению этих потерь, чтобы сократить время цикла. И эти меры оказались достаточно простыми для внедрения. Сотрудники «Энерго-Арсенал» очень быстро выработали решения, реализовали их и получили необходимый результат.
Александра Пученкина, руководитель проектов Регионального центра компетенций в сфере производительности труда
В условиях растущего спроса именно этот участок производства было решено оптимизировать в рамках нацпроекта «Производительность труда».
Что удалось сделать
Согласно данным предприятия, время значимой работы при производстве граненой опоры составляет 92 минуты, при этом время транспортировки занимает 50,5 минуты. Во время проработки потока выяснилось, что есть серьезные логистические ограничения, которые не позволяют повысить производительность. В итоге в ходе оптимизации переместили два станка плазменной резки на новый участок. И это сразу обеспечило феноменальный рост производительности, а время перемещений сократилось до 30 минут. Кроме того, на участке плазменной резки внедрили автономное обслуживание, что позволило повысить качество реза и также сократить время на дополнительную обработку деталей.
— Все реализованные процедуры дали нам очень сильный рывок. И знаете, после того как мы провели эту работу, мы поняли, что это еще не максимум. Есть еще что улучшить и где поднажать. У нас будто глаза открылись, и руки делают. Когда мы с ребятами с производства и из офиса рисовали поток, проходили совместное обучение, произошла такая синергия, мы очень сблизились. У нас систематизировались прежние знания, и теперь мы точно видим, как надо делать, чтобы получить эффект. И мы будем продолжать и на других участках составлять подобные карты потока, искать узкие места, чтобы повысить производительность внутри компании.
Дмитрий Вострецов, генеральный директор предприятия «Энерго-Арсенал»
Специалисты Регионального центра компетенций рассказали, что даже при общей вовлеченности коллектива в проект доля скепсиса у новых участников всегда присутствует. Кратный рост по некоторым показателям обычно действует на сотрудников убедительнее любых слов. В «Энерго-Арсенале» результаты тоже превзошли ожидания.
Культура бережливого производства
Несколько сотрудников предприятия прошли обучение и сертификацию и теперь будут дальше развивать культуру бережливого производства.
— Работа с сотрудниками «Энерго-Арсенала» была очень эффективной и достаточно легкой. Рабочая группа быстро поняла суть инструментов бережливого производства. Мы провели тренинги по программам непосредственно на предприятии, что сразу исключило разрыв теории и практики. Получается, каждый тренинг мы мгновенно адаптировали под предприятие и сразу шли и делали руками то, что требуется. Также хочу отметить высокую заинтересованность генерального директора, который принимал активное участие в реализации проекта на всём протяжении нашей работы. Для достижения поставленных целей это очень важно.
Александра Пученкина, руководитель проектов Регионального центра компетенций в сфере производительности труда
Для участия в национальном проекте «Производительность труда» можно зарегистрироваться на сайте. Заявку рассматривают до пяти рабочих дней.
Екатеринбург, ул. Конструкторов, 5;
технопарк «Университетский», оф. 2016;
тел. (343) 227-11-10.
www.frpso.ru
технопарк «Университетский», оф. 2016;
тел. (343) 227-11-10.
www.frpso.ru